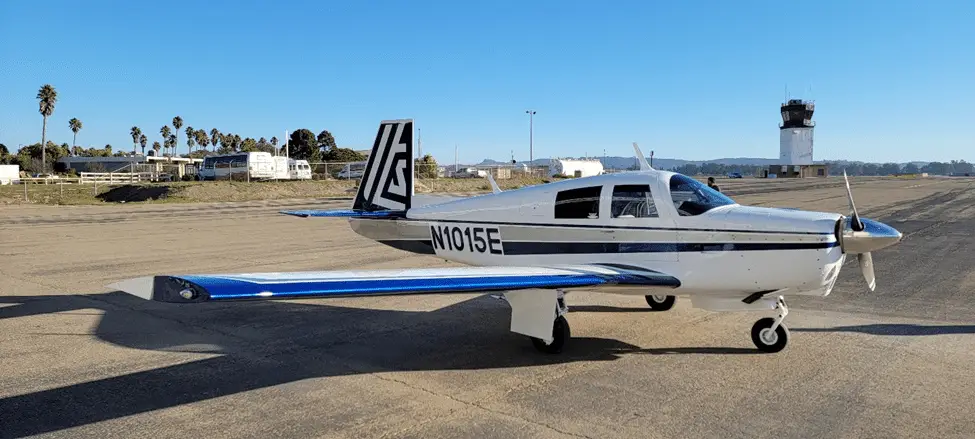
Sometime after seven weeks of not flying I really started feeling the withdrawal. From the time I took my first flight six and a half years ago I think the longest I had been without flying was 3-4 weeks and this felt like an eternity. The total downtime was roughly three weeks longer than originally anticipated, but if I had to make the decision again, I still would take the plane to Art Craft. You may be asking “Why, if it took so much longer than anticipated?” Keep reading and stick with me to the end, it will all make sense.
After reading reviews and looking at paint jobs by different shops I narrowed my choice down to two semi-local shops. I sent an email to one asking for a quote and waited. Two days later with no response I sent a follow-up email to which I received a one-page outline of work to be performed and a base price. The price was fair, but they were scheduling six months out and said they need the plane for a minimum of 6-8 weeks. A follow-up email received no response. When a company can’t find the time to respond to prospective customers it does not bode well.
You typically get what you pay for, and the work I had seen from Art Craft is much higher quality than the other shop I had contacted so I expected a higher quote. Following the “Buy the best and cry once” philosophy of an old friend, I sent an email to Art Craft. That same day I received back a very detailed 26-page quote outlining the entire process and what to expect. It was indicative of the professional manner in which they conduct business.
Their base quote was higher than the other shop, but there were things included in it that weren’t in the other quote, and with higher quality work it wasn’t really an apples-to-apples comparison. Their anticipated downtime of one month was much shorter, another plus. Finally, they would also be able to get me in the following month, and that sealed the deal. I added some additional items to the job, installing flap gap seals, removing some old antennas and installing flush panels to fill the holes, plus a few other things which added an anticipated 2-2 ½ weeks to the typical one month turn.
If you have a paint scheme, they can make it happen. It doesn’t have to be perfectly drawn out with a graphics program; they can work with a general idea. When I dropped the plane off Brenda showed me a Mooney they had just completed. It was beautiful! Then she showed me the hand drawn scheme they had used. The owner didn’t take an outline of a Mooney and draw his ideas on it, he had hand drawn the entire plane and then the lines he wanted and colored it in. It was anything but a professional-looking scheme. If the owner of that plane is reading this, please don’t take that the wrong way, because it was better than what I could have drawn. I mention it because they can literally work with any idea you come up with.
I had a general idea of the paint scheme I was looking for but needed some help getting what was in my mind onto paper, so Brenda put me in touch with Robert from Flight Lines Aircraft Paint Design. Robert was as much a pleasure to work with as Brenda and her crew. I sent him some pictures of some paint schemes I liked along with bullet points of what I like and don’t like.
Robert made the process easy and enjoyable. He initially sent back three different schemes for a starting point. From those I let him know which parts of each one I liked, which I didn’t, and he refined them and sent them back again. We traded emails back and forth with it getting closer and closer to what I was looking for. (Not an easy thing when I wasn’t exactly sure what I was looking for). I felt bad when I thought we had the final design, but then I saw a couple of other pictures and wanted to see another change. He gladly made the change and sent it back, now it was perfect.
When I dropped the plane off Brenda and her painter Tony met me and we went over the plane, then she gave me a tour of their facility. A couple days later I received the initial inspection report. To say it was “detailed” would be an understatement. It was 29 pages long and included 150 photos. That was followed up about a week later by the post stripping report that was 12 pages long and included an additional 47 photos. The reports left no questions about the condition of the plane, which repairs needed to be done, and which repairs fell in the “optional” category. This will likely be the only time the plane is painted in my lifetime, so I opted to fix everything, even the tiny blemishes. If you’re going to do it, do it right.
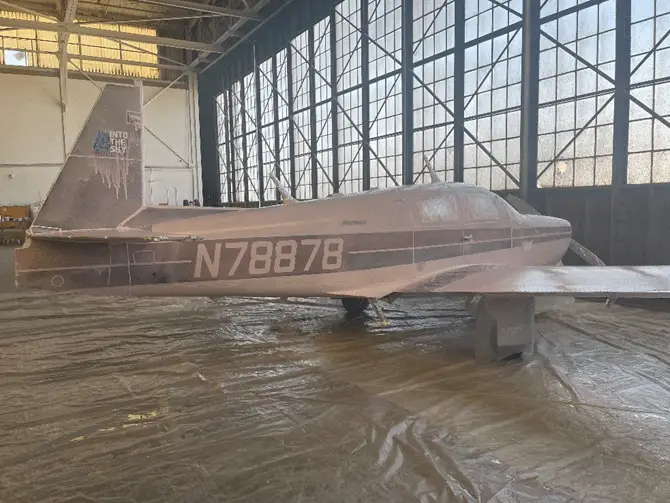
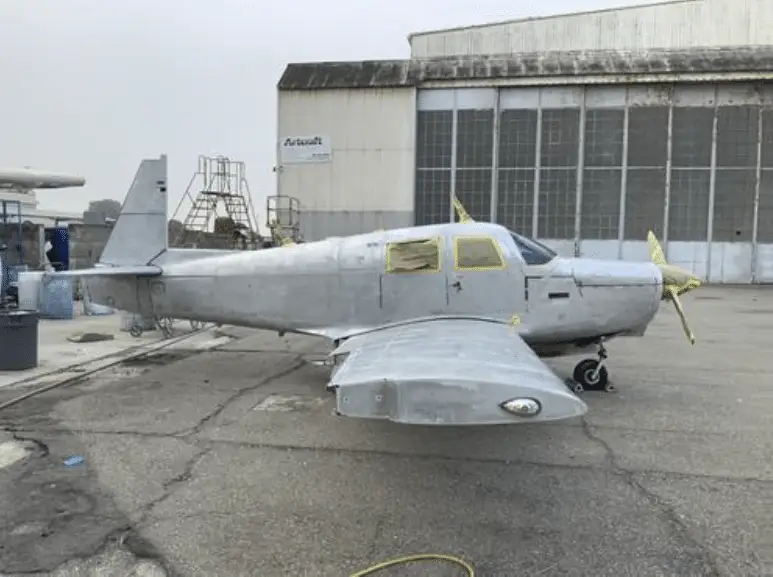
I’ll add a little side note about the repair times that are in the original quote and those that were added after inspections. The quote includes up to 10 hours of bodywork as part of the refurbishing process. Do not expect that time to be available for repairing hail damage, hangar rash, etc… Before spraying the paint stripper on, they tape all the seams. After the chemical stripping, they remove the tape from the seams and must remove that paint along the seams by hand. That process will eat up the allotted 10 hours and I’m sure that is the reason they include it in the quote. The times they quoted for the repairs on my plane were well within reason.
Writing a realistic review must include any negatives, so I’ll share the one negative from the experience. Perhaps this is just my expectation and not reality in the aircraft painting industry, but here you go. Communication at the beginning of the process, from initial contact, up through drop off, and the first couple weeks was amazing. Updates were provided unsolicited, and I felt well informed. After that, the communication slowed, and I had to reach out for updates.
In a phone conversation with Brenda later in the process she mentioned that she hadn’t sent out updates because they were just doing the body work and there wasn’t much to update. She likes to send photos and while pictures of the stripping process and the painting are exciting, I guess a picture of body work getting completed is not that exciting.
If I was to make a recommendation it would be to at least send out an email at the end of each week with a “this is where your plane is at right now” message. Even if the email only says, “we’re still working on repairing the body defects.” My ‘day job’ which pays for this amazing hobby of flight is CFO of three auto dealerships. Combined we service about 1,800 vehicles a month, and one of the metrics we measure our Service Advisors on is “Status Checks.” A status check is anytime a customer contacts them to find out the status of their vehicle. The goal is for the Service Advisor to call/email/text the customer a status update before the customer picks up the phone to call them.
Ok, back to your regularly scheduled glowing review.
“Hold on Richard, remember you said that it took about 3 weeks longer than it should have taken? What’s this ‘glowing review’ stuff you’re talking about?”
I know, I said stick with me to the end and all would be explained. There was an initial (subject to change) delivery date that came and went. I inquired of Brenda what the reason was for the delay. She explained that they had several employees that had called out in the previous weeks which put them behind. With almost 60 mechanics working in our shops, I can understand the predicament that put Art Craft in. There was a point earlier this year that one of our shops had a period of almost two weeks that all of our heavy-line techs were out sick and we couldn’t get any transmission or engine work done.
I am not going to hold those delays against them. Some things are out of your control, and you just do the best you can. That is exactly what Art Craft did, and why I would recommend them to everyone. The week before Thanksgiving I called and talked to Brenda again for an update. She said the plane was just about to go into paint. Then she outlined day by day what would be done and gave me the terrible news that it would be ready the day after Thanksgiving. I say terrible news because we were supposed to fly to St George, UT for Thanksgiving. St George is a two-hour flight or a six hour drive, but around the holidays that can easily turn into a ten hour drive.
The conversation went something like this:
Me: “We’re supposed to fly to Utah on Thanksgiving Day. That’s the difference between four hours in the plane or 20 hours in the car.”
Brenda: “That sounds horrible.”
Me: “I agree, do you want to drive with us?” (Said with a smile)
Brenda: “Let me talk with Teresa and see what we can do, I’ll get back to you later today.”
I hung up the phone, hopeful that something could be worked out. Later that afternoon I was back on the phone with Brenda and Teresa. They had talked with their crews and come up with a plan where they would come in on their days off to work on my plane and finish it up for delivery on the 23rd, the day before Thanksgiving.
“How confident are you in the plan?” I asked.
Teresa replied, “99.9% sure, but we can’t control acts of God.”
I thanked them for their willingness to go above and beyond to get it completed, knowing that the delays had been out of their control.
Monday morning Brenda sent me an email that they were still on track for a Wednesday delivery along with pictures of it primed, then the base white coat, and the stripes and graphics laid out. They were getting ready to lay the first color. More emails followed with more pictures, and it looked amazing! I felt like a kid waiting for Christmas to arrive.
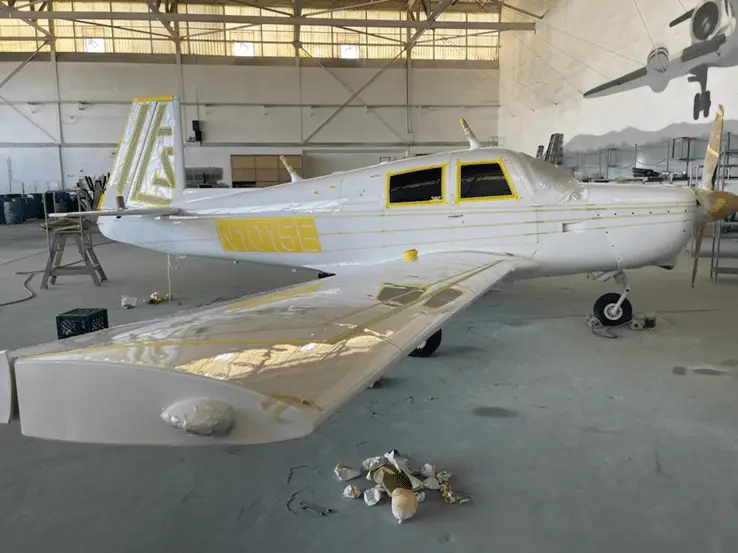
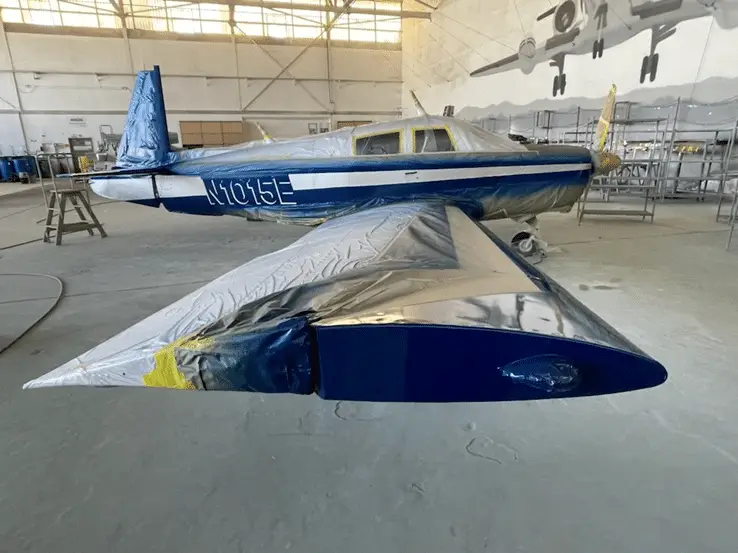
Finally, it was Wednesday and time to go pick up the plane. My friend Ken who had ferried me home from dropping it off was nice enough to give me a lift back to pick it up. The plane was beautiful. The blue looked even better than I envisioned, and when they pulled it out of the hangar and the sun hit the silver and blue, it was amazing. I couldn’t believe it was the same plane that I had dropped off. I walked around the plane inspecting the paint and especially all the control surfaces and linkages which had been removed during the process. Once all of that was done it was time for a photo shoot in front of the hangar. There was no rush, it was a “take all the time you want and let us know if something doesn’t meet your standards.” And if you missed something they have a one year warranty, just bring it back and they will fix it.
Finally, with an extremely thorough pre-flight completed and the plane fueled up it was time to fly. Lifting off the runway again after 9 ½ weeks felt wonderful. It was a smooth sunset flight back along the coast, some of the most beautiful flying you can do.
I said earlier that after my Art Craft experience, I would refer everyone to them. The quality of work was incredible. The job came in on budget. I did take three weeks longer than it should have, but that was due to things outside of their control. Putting together a plan with their crews who came in on days off to complete my plane making sure we were flying instead of driving to Thanksgiving meant everything to me. They could have just said “We’re really sorry,” but instead they found a solution. And don’t think they did it because they knew I would be writing up a review, I had never mentioned that to them. They did it because they are a great company and that’s what great companies do.
I don’t have any video of the process, but my friend Illya did a great job documenting his M20E getting painted by Art Craft. You can check out his videos here: https://youtube.com/playlist?list=PLT6CTlsO43126J-HBcb9gDpjxeWDc6XhM